Brochure
Download our document to see specific data of the service and how we work.
Let’s Start Work
Together
Please feel free to contact us. We will get back to you with 1-2 business days. Or just call us now.
CONTACT US NOW
Please feel free to contact us. We will get back to you with 1-2 business days. Or just call us now.
How can we help?
Maxwatt recognises that traditional steam turbines are not the best fit for low-pressure and wet steam energy recovery. These applications demand specialized design features to ensure reliability, efficiency, and minimal maintenance. Maxwatt offers an extensive range of energy recovery and waste pressure recovery turbines that come equipped with host of features.
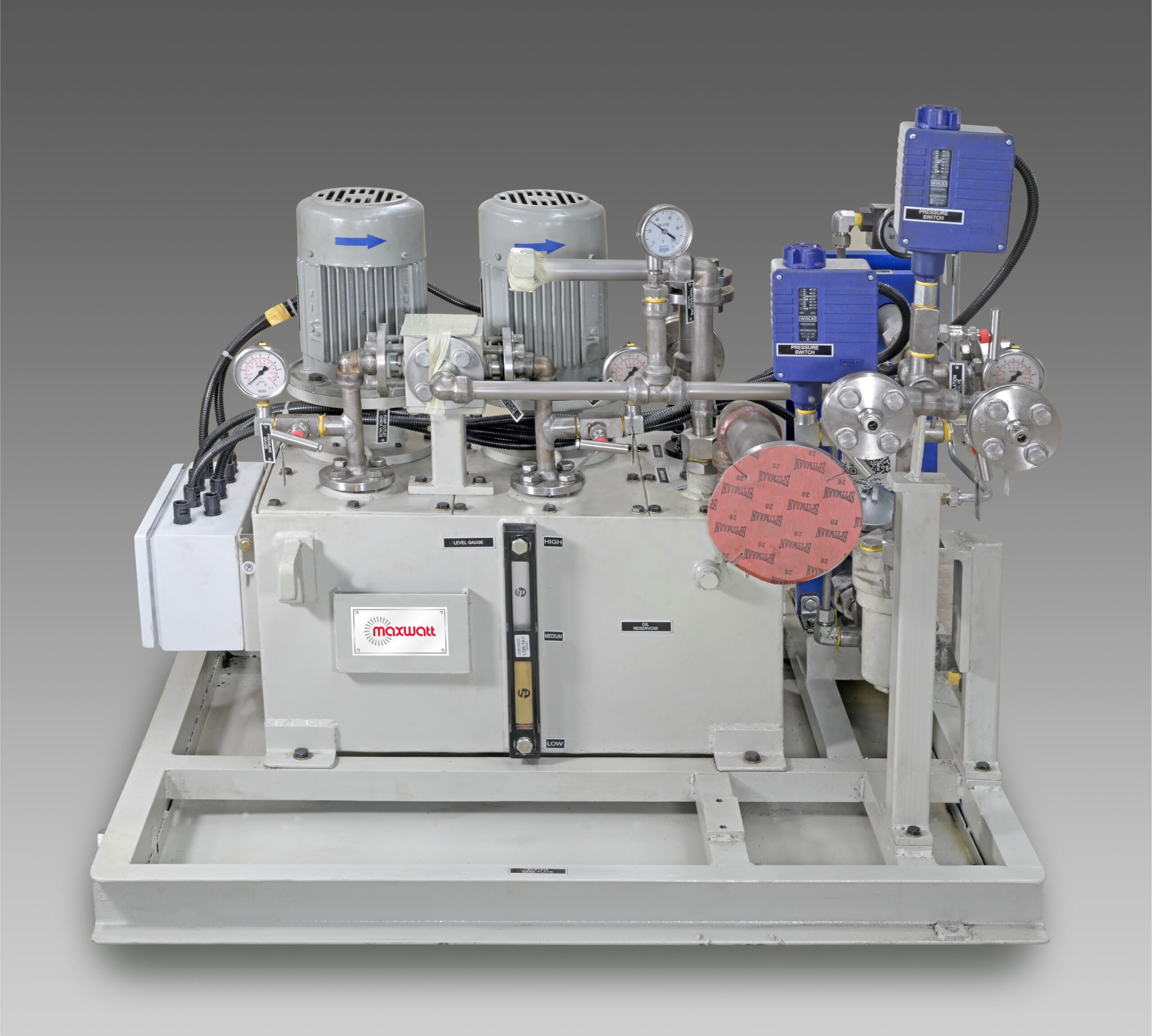
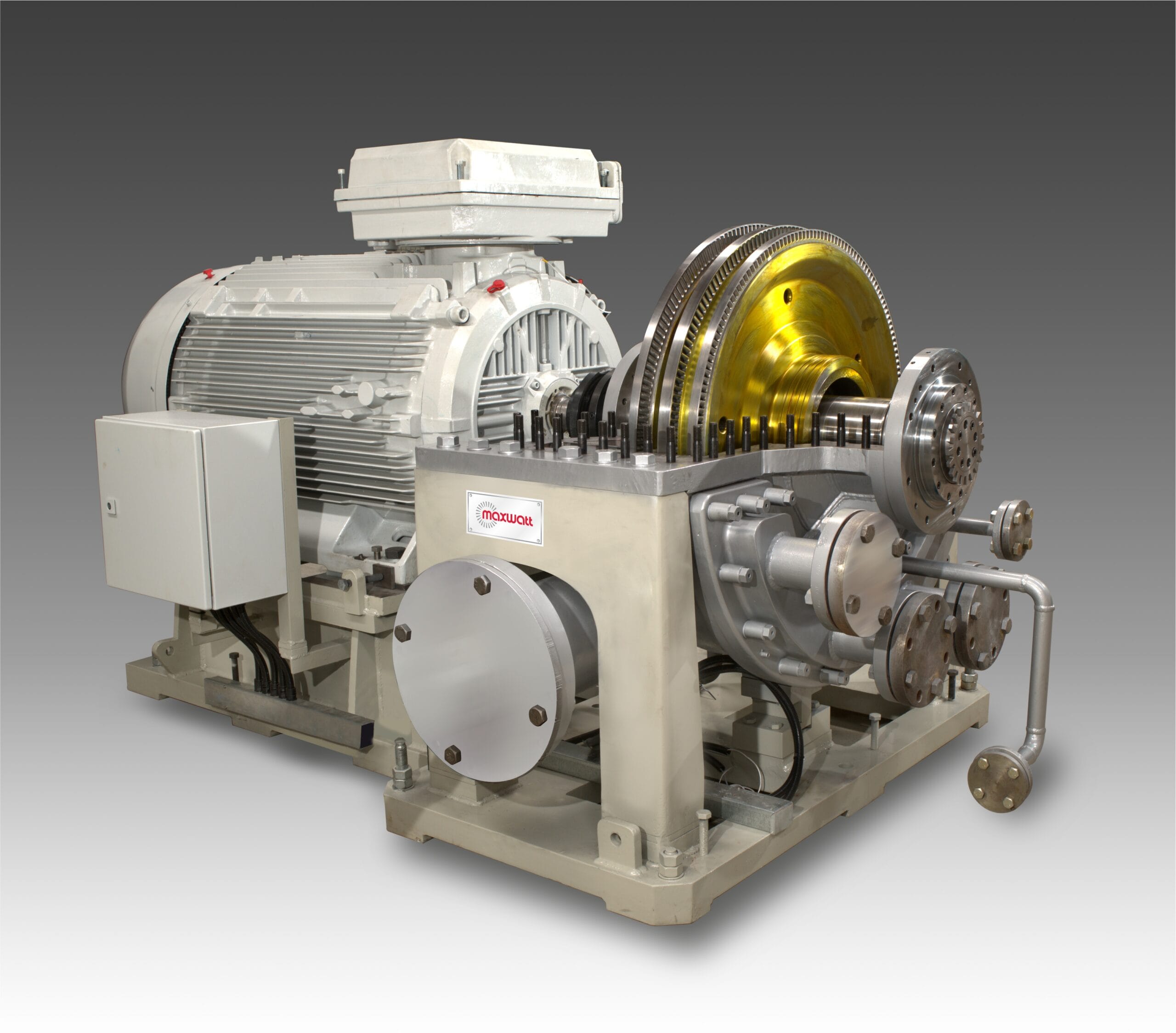
These machines use novel, well established & proven thermodynamic design & simulation tools to minimize no. of components resulting in a machine with no gearbox and a simple lubricating oil system. Our objective was to provide Industry a machine that offers high efficiency, ease of operation & lower maintenance requirements.
Model and Rating
- Type - Impulse
- Configuration - Back Pressure / Condensing
- Extraction - With / Without Extraction
- Nominal Rating - Up to 3,000 KW – Direct Drive, Up to 10,000 KW – Geared Drive
- Inlet Steam Pressure - Up to 30 Ata
- Inlet Steam Temperature - Up to 300°C
- Maximum Exhaust Pressure - Up to 15 Ata
- RPM - Up to 6,000
Unique features of Maxwatt ERS / Micro Turbines
Double Pedestal Construction
Direct Drive – No Gear Box
Direct integration of the turbine and generator results in a more compact footprint and low speed simplified rotating train.. This gives several advantages like over conventional design like –
- Elimination of a sophisticated forced-feed lubrication system as major oil consumer Gear Box is not present.
- Lower maintenance – No need to maintain stock of expensive Gear Box Bearings, Oil baffle, Large Oil Pumps etc.
- Compact and simple package requiring lower maintenance.
Tailored Multi-stage Design for High Efficiency
These turbines employ a multistage design customized to suit specific steam conditions, offering unrivalled efficiency that outperforms any single-stage turbine. The benefit of this design is a faster payback period.
This feature paired with double-bearing construction, results in a heavier rotor that effectively manages frequency fluctuations caused by fluctuating steam demand of the process.
Rivet-less Bladed Design
- Improved Blade life as there is no blade stress which is caused in a riveted bladed design.
- Reduced Disc clearances leading to better efficiency.
Multi-Control valve option for more efficient Part Load operation
Common Base Frame
Installation using Anti Vibration Mounts - No requirement of specially designed Civil Foundation
Induction Generator for simplified plant connectivity & parallel operation with Grid
Fully Automatic control system
- Push Button automated start sequence.
- Push Button or Automated shut down control
- Monitoring of all important functions, parameters with fault.
Remote Monitoring through IOT App
Attribute | Details |
---|---|
Type | Impulse |
Configuration | Back Pressure / Condensing |
Extraction | With / Without Extraction |
Nominal Rating | Up to 3,000 KW – Direct Drive Up to 10,000 KW – Geared Drive |
Inlet Steam Pressure | Up to 30 Ata |
Inlet Steam Temperature | Up to 300°C |
Maximum Exhaust Pressure | Up to 15 Ata |
RPM | Up to 12,000 |